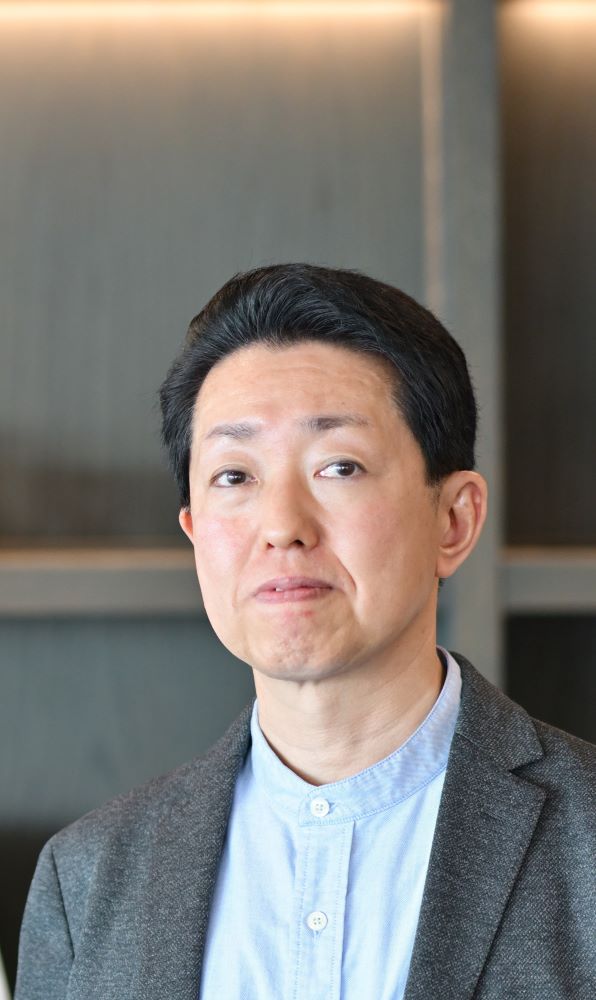
デジタル活用を含む企業変革、人的資本経営、組織開発、変革人財育成のコンサルティング案件に従事。20年を超える様々なコンサル経験を活かし、製造業や卸売業、サービス業等のお客様に対して支援を行っている。 対話型組織開発、キャリア開発、リスクマネジメント、サービス品質マネジメントの知見・スキルも有する。(2025年2月時点)
「手の届きやすい範囲」の限界
――「DXを進めているはずなのに、変革が進まない」という相談が増えてきました。背景には何があるのでしょうか?
青地:
「2025年版ものづくり白書」によると、『デジタル技術を活用した業務改善に取り組む事業者の割合は80%に達するものの、新規製品・サービスの創出や顧客基点の価値創出によるビジネスモデルの根本的な変革、企業文化および組織マインドの根本的な変革において成果を創出しているのは20%前後』に留まっていますね。
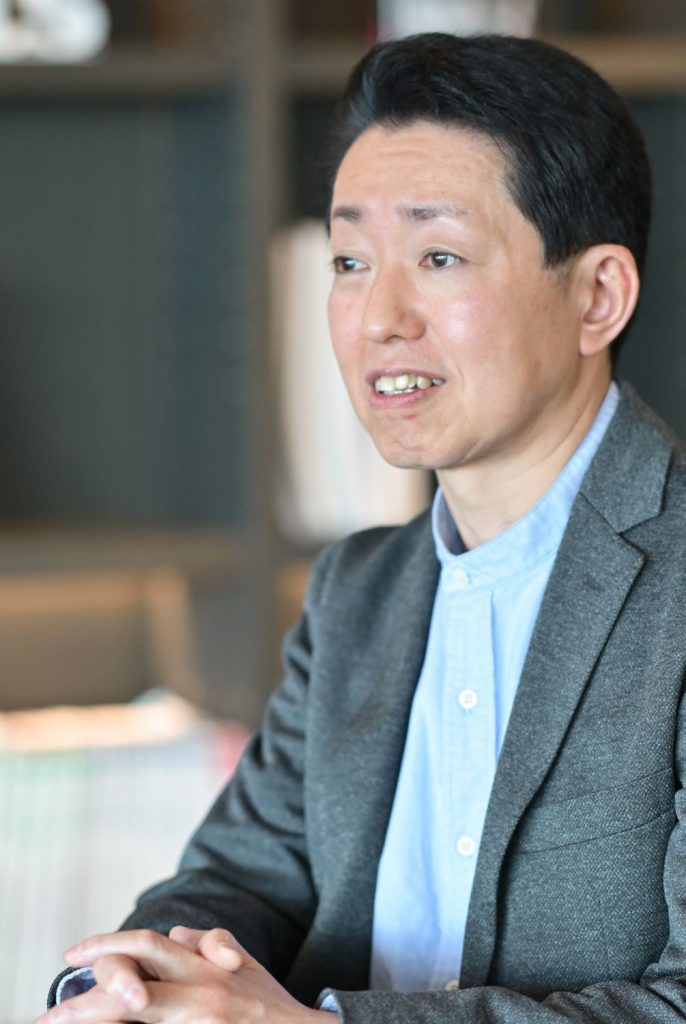
https://www.meti.go.jp/report/whitepaper/mono/2025/index.html
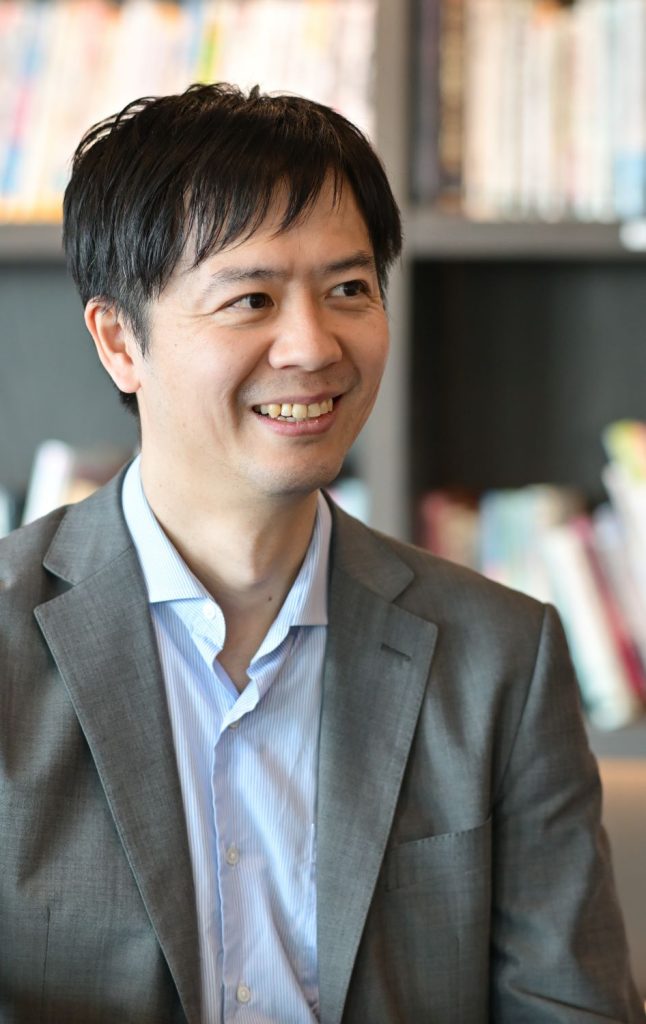
島野:
これまで「一部の部門での取り組みや、部署ごと・個別工程ごとの改善」に留まっていたものが、次第に「製造機能の全体最適」や「事業機会の拡大」といった競争力の強化を目指す取り組みに移行しつつあるものの、まだまだ成果を出すまでに至っている企業は多くはないという実態を現していると思います。
青地:
そうですね。コンサルの現場に入ってみると、DXの推進部署や現場の担当者が「自分たちの手の届きやすい範囲」で変革活動に取り組むケースがまだまだ多いです。解決したい課題を伺うと、本来は顧客と直接つながるエンド・トゥー・エンド(e2e)のプロセス変革が必要であるのに、このような複数部門が関与する活動は敬遠され、部門個別最適に陥っているケースが見られます。
大切なのは「問い」から始めること
――では、どのようにしてDXを設計すべきでしょうか?
島野:
DXという言葉が先行するあまり、手段が目的化し、「事業戦略との接続」や「課題の構造理解」が置き去りになっていることが多いのです。私たちがご支援している現場でも、「課題の解像度が低いまま、ツール導入のスケジュールだけが進む」といった状態は決して珍しくありません。大切なのは、“何を実現することを目的に、どの課題を、どのように変えたいか”という「問い」から始めることです。
青地:
私たちは「ものづくり領域」における情報戦略策定において、「事業課題を基点」としたアプローチを提案しています。簡単に言えば、まず「チェーンごとの課題」を経営戦略/事業戦略を基に具体化し、「生産機能への要求」を整理します。次に、「To Be像」を描き、その状態を実現するために必要な「データと仕組み」を洗い出します。その上で情報戦略やその後の推進体制を設計するものです。
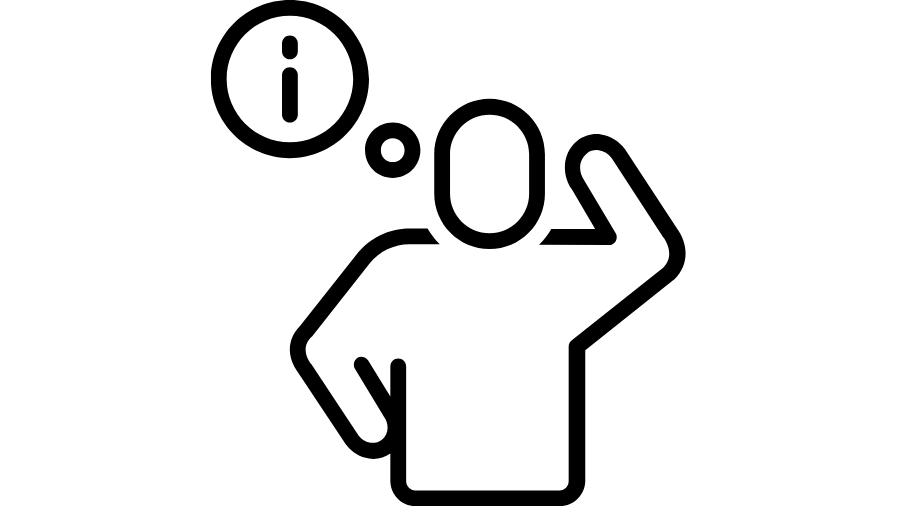
――「事業課題を基点」とした企業変革を実践する上で、製造業ならではの難しさはありますか?
島野:
まず、社風にもよるのですが、製造業では現場が強い権限を持っていることが多く、全社で一律の仕組み・ルールを展開することが容易ではない点が挙げられます。また、製造現場では「失敗しないこと」が当たり前となっているために、「仮説検証」を前提にした事業課題基点のアプローチに心理的な抵抗感を示すケースも見受けられます。
青地:
DXを全社レベルで推進していく中で、多くの製造業が直面するのが「現場任せによる部分最適化」の課題です。製造現場の自発性は非常に高いのですが、それぞれが独自に取り組みを進めることで、データ構造や仕組みがバラバラになり、共通化やナレッジの利活用が難しくなってしまいます。現場主導のデジタル施策が乱立し、個別に最適化されていると、将来的な変革活動の“足かせ”にもなりかねません。
戦略の方向性と現場をつなぐ接着剤
島野:
多くの製造業では、「改善文化」が深く根付いています。それ自体は良いことなのですが、現場の改善活動と同じような感覚でDXに取り組んでしまうと、短期的な成果は出せたとしても、中長期的な視点では全社的に整合を図るための“再設計“や”やり直し”が必要になったりします。このような後戻りを防止し、全体最適を担保するために必要なのが、CoE(Center of Excellence)という“横ぐし機能”です。
――CoEについて、もう少し詳しく教えてください。
青地:
CoEは簡単に言えば「戦略の方向性と現場をつなぐ接着剤」です。本来、情報戦略の策定と実行は、事業を推進する主体である事業部門が一義的に担うべき役割です。しかし、事業部門毎または拠点毎の個別最適の積み上げでは、企業全体の価値創出や中長期の競争優位の確立にはつながりません。こうしたギャップを埋めるために、CoE組織を設置することが一案となります。
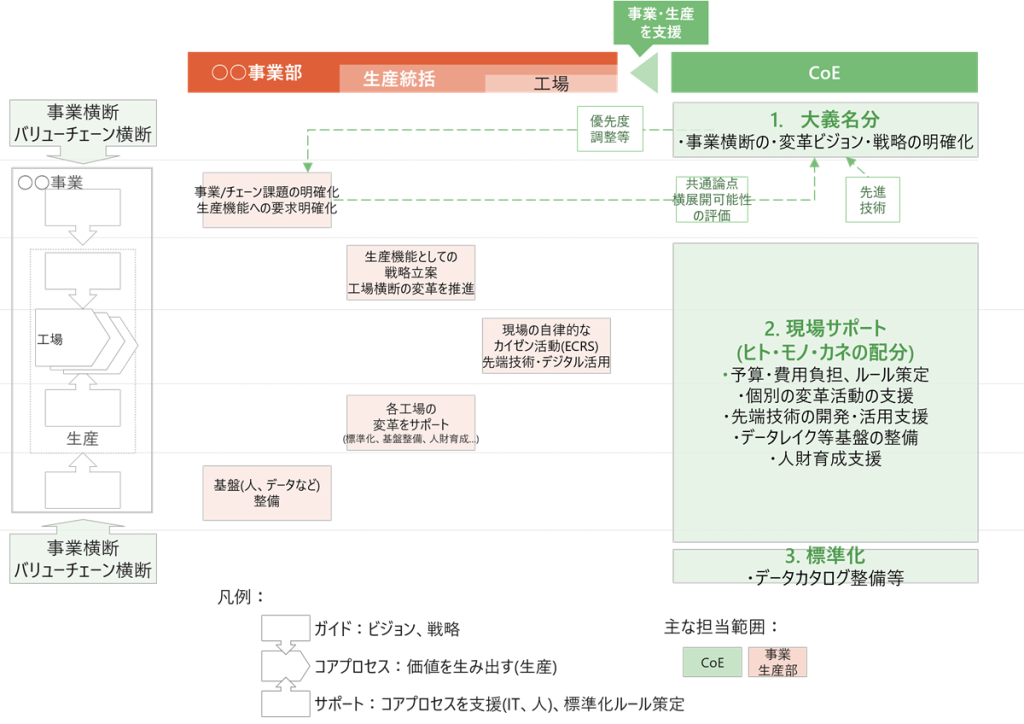
島野:
私たちはお客様企業の情報戦略策定において、以下の3つの機能からなるCoEの設置をご支援しました。
1つ目は大義名分の明確化。これは、戦略の意図や狙いを、現場にとっての意味・意義として“翻訳”する役割です。「なぜこの取り組みを行うのか」「自分たちにどんな価値があるのか」をきちんと腹落ちさせることで、現場の納得感と主体性を引き出します。
2つ目は現場サポート。活動に必要なヒト・モノ・カネを適切に配分し、現場のボトルネックを解消します。例えば、情報基盤が整っていない工場に対して、共通の技術支援を行う。
3つ目は標準化とガバナンスの推進。バラバラに進む個別プロジェクトを、一定の共通ルールや設計思想・基準で束ね、再現性と横展開性を確保するための機能です。
組織知を高める“学習インフラ”
青地:
「共通基盤を整える」ことを先送りにしたことで、後から膨大な再構築コストが発生してしまった企業もあります。早期の段階で、どこまでを個別に任せ、どこを共通化すべきか、その“線引き”をしておく必要があります。そのためにも、CoEには「標準を定義する」だけでなく、「対話を通じて合意を形成する」ことが求められますね。
――標準化というと、硬直的な印象もあります。現場の創意工夫とどう両立させればよいのでしょうか?
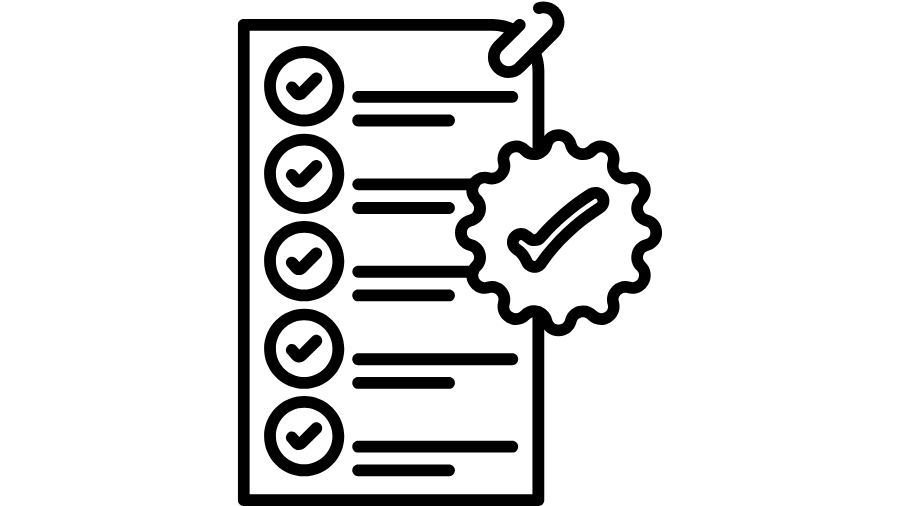
島野:
確かに、標準化という言葉にはネガティブな印象を持たれがちです。しかし、ここで重要なのは、「自由と秩序のバランス」です。現場の裁量を活かしながら、全社のフレームの中で自由に動ける状態を設計する。CoEはその“土台づくり”を担うべきです。また、ある取り組みが特定の拠点でうまくいったら、それを他の拠点にも展開できるよう支援する。単なる横展開ではなく、「どうすればそのやり方が他でも再現可能になるか」を一緒に考えるのが役割です。
青地:
私たちは、CoEを単なる推進機関ではなく、組織知を高める“学習インフラ”として位置づけています。成功事例だけでなく、失敗事例に対しても、「なぜ失敗したのか」「何が成功要因だったのか」を組織知として整理し、同じような失敗を繰り返さないようにする。ナレッジが溜まり、学習サイクルが回れば、活動は一過性のプロジェクトではなく、進化するための基盤となり得ます。
変革活動が持続できている組織には、それが正式なCoE組織ではなくとも、同様の機能・役割を担っている人々と、それらを支える土台としての組織カルチャーがあると考えています。
(下)では、「人と組織が変わらなければ製造業DXは定着しない──人が成長し、やりがいを持てる工場」の実現に向けて」をテーマに、人と組織の視点から考察します。